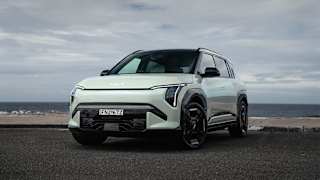
Melbourne's role in EVs
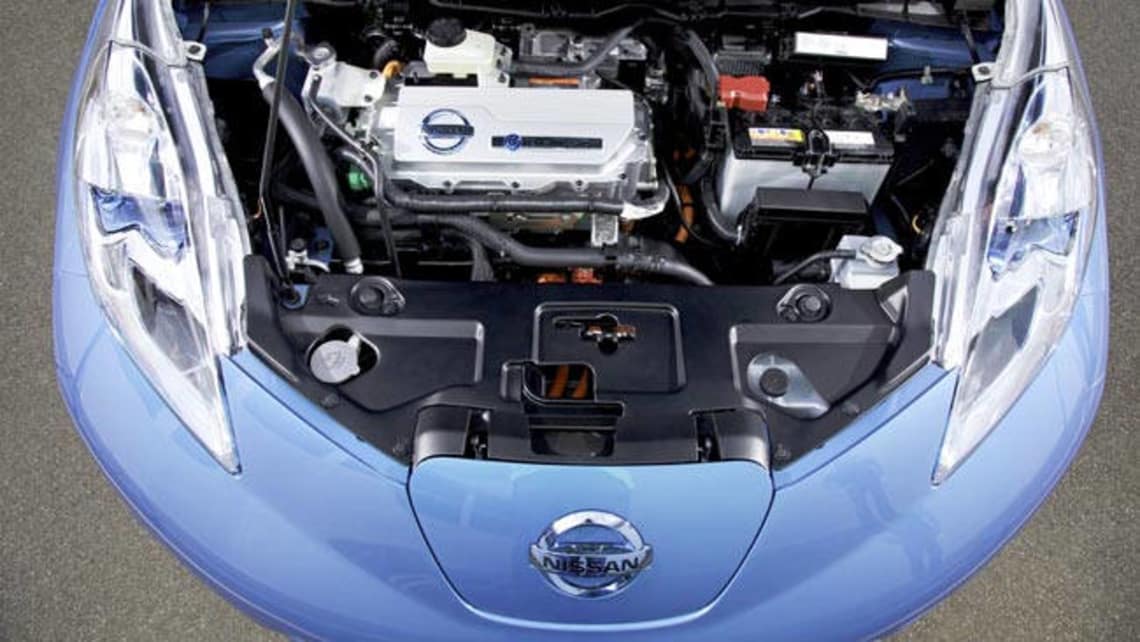
... begin making components for zero emission electric vehicles sold around the world. Manufacture of aluminium components for the Nissan Leaf electric vehicle begins at Nissan Australia’s Dandenong casting plant in mid-2012.
A $21m investment in tooling and plant upgrades is already well underway, with some $3.3m provided by the Federal government’s now defunct Green Car Innovation Fund, and further support from the Victorian Government’s Business Assistance Grant.
The contract involves the production of aluminium components used in Nissan’s Leaf electric car – already on sale in US, Japan and UK and destined for Australia in mid-2012.
Components to be made in Melbourne include an inverter case, inverter water jacket and water jacket cover. The inverter is a key part of the Leaf’s electrical operating system and the Dandenong plant will eventually manufacture around 22,000 inverter castings per month for export to Japan, the UK and the USA.
The Leaf emits zero tailpipe emissions thanks to its all-electric power train with a battery charged by connecting the car to mains electricity. Nissan Australia is currently participating in the Victorian government’s five year electric vehicle trial.
The company has supplied a fleet of 16 pre-production Leafs for use by Victorian householders, who each will live with the cars for three months.
Nissan’s Dandenong casting plant which employs around 160 Victorians is enjoying a period of growth following the announcement in October that it would also begin manufacturing a range of vehicle accessories including nudge bars, tow bars and sports bars.
The accessory manufacturing business was won from Asia and secured 20 full time jobs. The casting plant was founded in 1982 but was forced to reinvent itself as a stand-alone supplier following Nissan’s withdrawal from local automotive manufacturing in 1991.
Comments